▣ Overview of the Piping Design Management System
1) Design Requirements, Scope, and Specifications:
Verify the design requirements, scope of work, and special conditions outlined in the contract. Prepare design drawings, schedules, and progress management for comprehensive design work, establishing standards, procedures, and management techniques.
2) Planned Design Schedule:
The planned design schedule is organized by level and operates systematically, summarizing various information from lower-level tasks to higher levels.
– Level I: Main schedule showing timelines and tasks for design, procurement, construction, and commissioning.
– Level II: Summary schedule displaying interrelationships between unit tasks across the entire process.
– Level III: Baseline schedule serving as the basis for process management for each unit task.
3) Design Progress Management:
Establish criteria for determining the design progress rate based on the critical path affecting the entire process, assigning weights according to the characteristics of each unit design task.
4) Design Meetings:
To ensure efficient and prompt execution of design tasks, regular or ad-hoc meetings should be conducted to discuss and confirm overall design work.
Monthly Progress Meetings: Regular meetings to review and inspect the overall flow of design progress. Plans and progress should be documented and submitted on a monthly basis.
Weekly Progress Meetings: Regular meetings to document and discuss design progress and issues on a weekly basis.
Special Progress Meetings: Ad-hoc meetings to resolve specific design issues or problems, establishing solutions and countermeasures.
Meeting Minutes: Discussions from design meetings should be recorded in minutes for continuous review and monitoring until unresolved issues are settled.
⋅
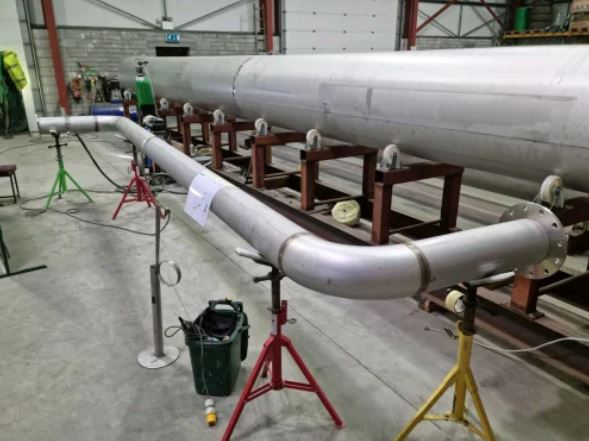
▣ Planned Piping Design Schedule
1) Planned Design Schedule:
To ensure that the design work progresses according to the planned schedule, it should be organized by unit tasks.
2) Functions of the Planned Schedule:
The planned schedule serves the following functions from the perspective of process and progress management:
– Provides detailed schedules for each unit design task.
– Basis for calculating progress rates, analyzing performance, and forecasting progress.
– Basis for assessing the status of design progress and overall project progress.
– Provides related information linked with construction process management systems.
– Basis for reporting design progress.
– Reference for verifying the sequence of tasks between related departments or companies.
3) Operation of the Planned Schedule:
To systematically manage the schedule and submission of deliverables, a planned design schedule should be created and operated to ensure the design process progresses according to the planned schedule.
▣ Management of Design Progress Rate
1) Establishing and Distributing the Progress Rate Calculation Method:
To manage the design progress rate accurately, develop a progress rate calculation method, consult with the client, finalize, and distribute it to related departments (managed on a weekly and monthly basis).
2) Design Progress Rate Management Method:
Calculate the design progress rate by applying a weighted progress rate calculation standard, multiplying the achievement rate by the weighted value for each design task.
3) Design Progress Rate Calculation Standards:
Assign weight values to each unit task (Activity) and calculate the progress rate based on the achievement rate compared to the planned schedule.
Overview: The basic elements for calculating the design progress rate include the weighted value for each unit design task (Activity), the achievement rate of unit design tasks, and the progress rate.
Weight Value Setting: Weight values are assigned based on the manpower (M/H) required for each deliverable or the complexity and amount of each unit task. Weights are distributed among key deliverables.
▣ Review and Approval of Design Documents
1) Review and Approval of Design Documents:
Review and verify that design documents reflect all applicable codes, standards, design requirements, and conditions.
2) Types of Design Documents:
Basic Design Documents: Based on the basic plan and environmental impact assessment, these documents form the foundation for designing main equipment and auxiliary facilities and conducting technical evaluations.
Detailed Design Documents: Developed from basic design documents, these detailed documents include all necessary design information for manufacturing and construction, reflecting the characteristics of main and auxiliary equipment.
3) Submission Purposes for Design Documents:
– For Review and Reference: Submitted for pre-review and feedback before finalizing design documents to ensure efficient design execution.
– For Approval: Submitted after internal review and verification to obtain the client’s approval.
– Final or Construction Submission: Submitted for construction purposes after obtaining final approval from the client, and provided to both the client and manufacturing or construction contractors.
4) Review Contents of Design Documents:
Design documents should be checked against a checklist, circulated among relevant departments for feedback, and, if necessary, verified by experts before submission.
▣ General Guidelines for Preparing Design Documents
1) Overview:
To standardize the preparation of design documents and drawings, establish minimum standards for format, notation, paper size, technical content, and units of measure.
2) Scope of Application:
Follow the same standards and procedures for issuing and revising various design documents and drawings.
3) Application Requirements:
All companies must apply the same standards and procedures for preparing design documents and drawings, ensuring the following information is included in the Title Block (using SI Units):
– Document and drawing number
– Document and drawing title
– Revision status and date
– Project name, client name, and design service company name
– Names or signature fields of the document/drawing preparer, reviewer, and approver
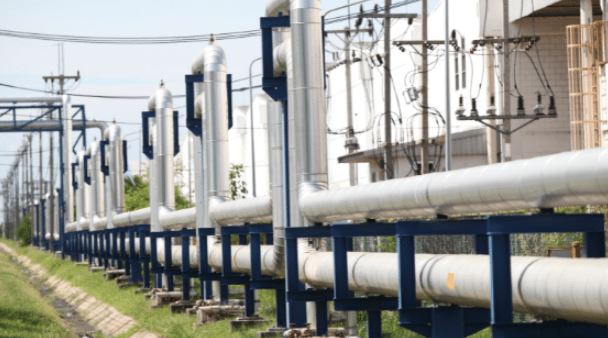
⋅
▣ Piping Design Drawings
1) Overview:
Design drawings, essential for plant construction, must meet minimum requirements for preparation and management.
2) Scope of Application:
All companies must follow the same standards and management system for preparing, issuing, and revising design drawings.
3) Classification by Drawing Purpose:
– Design drawings are classified into three types based on their purpose:
– Sketch Drawings: Document design concepts or research results (not formal drawings).
– Preliminary Drawings: Issued for client consultation, review, or bidding purposes.
– Design Drawings: Issued for manufacturing, installation, and construction purposes.
▣ Management of Piping Design Outsourcing
1) Overview:
To ensure high- quality deliverables, detail the outsourcing process, including scope of work, responsibilities, criteria for selecting and evaluating vendors, and management systems.
2) Key Considerations for Outsourcing Design Work:
Establish criteria for selecting the best vendors and thoroughly manage the review and approval of submitted design documents and drawings.
3) Management Plan for Design Outsourcing:
– Develop a plan for managing outsourcing efficiently, focusing on quality and resource management.
– Quality Management Plan: Ensure timely submission of high-quality design deliverables.
– Resource Management Plan: Prevent changes in design personnel and involve qualified personnel in the design process.
4) Directions for Outsourcing Design Work:
– Emphasize preventing design errors, improving quality, and adhering to the design process.
– Maintain consistency in the scope of work and adherence to the design process.
– Comply with the technical content of design standards.
– Support effective personnel management and operation of the outsourcing company.
– Empower the project manager with responsibility and authority, requiring weekly and monthly work reports.
– Conduct design verification by experts to prevent errors and improve quality.
– Foster horizontal cooperative relationships and minimize revision work on design content.
5) Pre-Evaluation of Design Outsourcing Companies:
Criteria for Selecting Design Outsourcing Companies:
– Expertise in the Field: Select vendors with expertise and a proven track record.
– Design Service Cost: Select vendors capable of performing within the design budget.
– Capability to Perform Services: Select vendors with the capability to perform design services.
– Contribution to the Company: Select vendors that prioritize company guidelines and performance.
– Client-Recommended Vendors: Select vendors recommended by the client for smooth execution.
– Pre-Evaluation Documentation for Design Outsourcing Companies:
Review the scope of work, quality improvement plans, similar project experience, technical staff and qualifications, dedicated design and quality assurance teams, and documentation required by other design service companies.
– Performance Evaluation and Management of Design Outsourcing Companies:
– Conduct quarterly evaluations to manage design outsourcing companies efficiently, assessing:
– Compliance with quality control procedures using checklists for design deliverables.
– Timely preparation and adherence to delivery schedules.
– Frequency and ratio of document revisions due to design errors.
– Technical level and turnover rate of design personnel.
– Compliance with the technical content of design guidelines.
– Proper execution of design instructions and work guidelines.